Mit 3D-Druck den Turbinenbau voranbringen
Erkenntnisse von der 5. ICTM Conference 2019 in Aachen

Mit 3D-Druck den Turbinenbau voranbringen
Erkenntnisse von der 5. ICTM Conference 2019 in Aachen
Additiv: Per 3D-Druck entsteht das sogenannten Boroskopauge der schnelllaufenden Niederdruckturbine des MTU-Getriebefan-Triebwerks des Airbus A320neo. (Bild: MTU)
Die Energiewende im Flugverkehr und der Energieversorgung steht und fällt mit einer neuen Form des Turbinenbaus. Ein wichtiges Mittel zum Zweck ist der metallische 3D-Druck.
Die Botschaft der 5. ICTM Conference 2019, der Tagung des International Center for Turbomachinery Manufacturing in Aachen, war klar und ein ehemaliger Siemens-Vorstand fasste sie in zwei mahnenden Sätzen zusammen: «Ein wirklicher Innovationssprung kann nur aus dem Gebiet des Additive Manufacturing (AM) kommen. Doch dazu müssen Fertigungstechniker mit Materialentwicklern und Turbinendesignern interdisziplinär zusammenarbeiten.»
Das scheinen sich mittlerweile alle namhaften Turbinenhersteller weltweit zu beherzigen und setzen sie in die Tat um: MTU Aero Engines etwa zählt zu den Pionieren bei dem Einsatz von Additive Manufacturing (AM) im Triebwerksbau. Im Flugzeugeinsatz befinden sich bereits rund 2000 seriengefertigte AM-Niederdruck-Turbinenteile, die das ICTM-Mitglied der ersten Stunde per selektivem Laserschmelzen (SLM) herstellt. Kurz bevor steht der Start von weiteren additiv gefertigten Bauteilen mit einem Volumen von 25‘000 bis 30‘000 Komponenten pro Jahr ab dem Jahr 2020.

Laserauftragsschweissen für die strukturelle Reparatur
Zu den Pionieren zählt auch das Unternehmen Siemens, das den 3D-Druck vor allem in seiner «Power and Gas Division» einsetzt. Der Konzern serialisierte bereits mehr als 15 additiv gefertigter Bauteile mit der enormen Erfahrung von mehr als 150‘000 kumulierten Betriebsstunden bei Kunden im kommerziellen Einsatz. Diese Erfahrung setzt Siemens für die Brennerentwicklung der neuesten Gasturbine – der Siemens SGT-9000HL Klasse – ein, um den Wirkungsgrad zu steigern und somit den CO2-Ausstoss zu senken.
Im Geschäftsfeld «Maintenance, Repair and Overhaul (MRO)» bei der «Power and Gas Division» am Siemens-Standort Berlin leitet Dr. Bernd Burbaum Forschungs- und Entwicklungsprojekte als «Advisory Key Expert Joining and Repair». Als Siemens-Erfinder des Jahres 2017 wurde der Inhaber von 65 Patenten ausgezeichnet für die Entwicklung eines Laserschweissverfahrens für Gasturbinenschaufeln. Bei der Reparatur von kritischen, stark belasteten Gasturbinen-Komponenten hat sich bei Siemens LMD bewährt.
«Wir setzen das Laserauftragsschweissen für die strukturelle Reparatur von Heissgaskomponenten ein», erklärt Burbaum. «Als limitierend empfinde ich die Aufbaurate. Hier gibt es noch Optimierungsbedarf vor allem beim Einsatz an grossen Komponenten.» Bewährt haben sich hier als LMD-Pulver nickelbasierte Superlegierungen mit hohem Anteil an intermetallischen Ausscheidungen (γ'-Phasen).

Additives Design erhöht Schaufel-Performance
Auch die MAN Energy Solutions SE aus Oberhausen ist kein Newcomer in Sachen 3D-Druck (LPBF). Das ICTM-Mitglied stieg mit Hilfe des am Fraunhofer ILT entwickelten und patentierten Verfahrens «Laser Power Bed Fusion LPBF» (früher bekannt unter dem Begriff SLM) in den metallischen 3D-Druck ein. Bewährt hat sich LPBF nicht nur beim Prototyping, sondern auch schon beim ersten zugelassenen Serienbauteil: So liessen sich die Produktionskosten für das Bauteil einer Verdichterschaufel senken, weil es nicht mehr aus 13 einzelnen Teilen, sondern direkt als eine Komponente entsteht. Für das Verfahren spreche ausserdem, dass sich mit Hilfe des Additive Designs die Konstruktion optimieren und die Performance der Schaufel steigern liess.
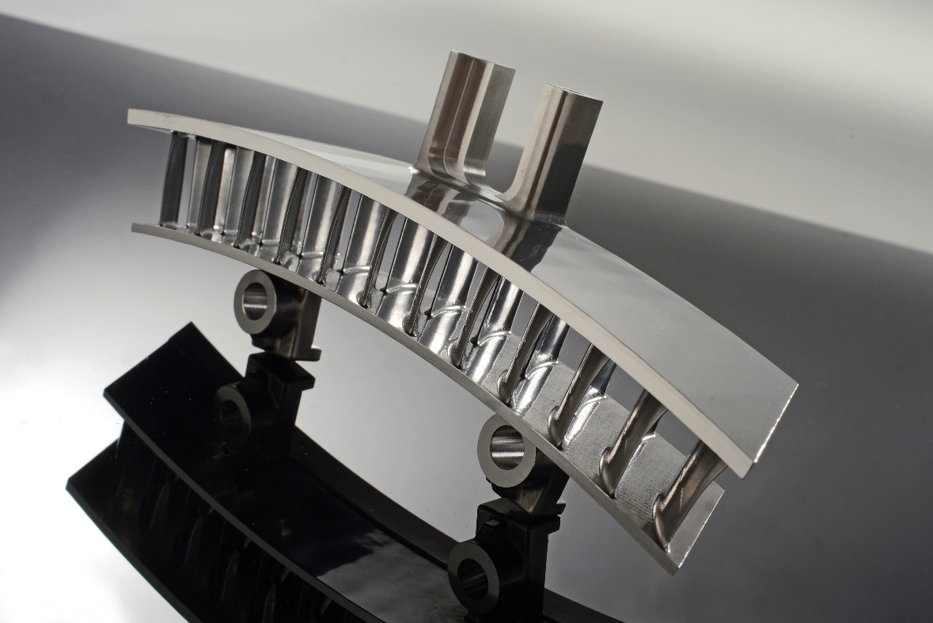
Mehr als 50% der Belichtungszeit einsparen
Anders Such kümmert sich in Oberhausen als neuer Leiter des Bereichs LPBF um den metallischen 3D-Druck, der die Produktivität im Turbinenbau steigern soll. Testläufe des langjährigen Fraunhofer ILT-Mitarbeiters an unterschiedlichen Systemen ergaben, dass sich durch eine geschickte Anpassung der Prozessparameter die Aufbauraten (> 12 mm³/s) bei gegebener Prozesssicherheit auf kommerziellen Anlagensystemen erhöhen lassen.
Im Detail liessen sich der 3D-Druck von Leitschaufel-Segmenten durch die Änderung der Prozessparameter von 200 W (Schichtdicke: 20 µm) auf 400 W Laserleistung (Schichtdicken: 40 bis 120 µm) von 26,14 auf 7,57 Stunden senken. Such: «Wir können mit der Anpassung der Prozessparameter mehr als 50% der Belichtungszeit einsparen.» Im nächsten Schritt folgt die Überführung dieser Methode in die Serie.
Seltenen Zertifizierungen nach Nadcap
Doch nicht nur grosse Konzerne mischen in Sachen metallischer 3D-Druck mit, auch Mittelständler sind in diese Zukunftstechnologie eingestiegen: Dazu zählt zum Beispiel die 1989 gegründete MBFZ Toolcraft GmbH aus Georgensgmünd bei Nürnberg (rund 400 Mitarbeiter), in der sich Christoph Hauck als einer von insgesamt drei Geschäftsführern auch um das Thema AM kümmert.
Spezialisiert ist das Familienunternehmen auf die Fertigung von Präzisionsteilen, Baugruppen, Werkzeugen und Spritzgussteilen. Intensive Erfahrung hat der Full-Service-Supplier, der zehn AM-Anlagen plus Peripherie für zwölf Millionen Euro besitzt, bereits mit dem metallischen Laserschmelzen im Pulverbett gemacht. Dabei arbeitet das Unternehmen eng zusammen mit Siemens und Trumpf.
Die Kunden der Mittelfranken kommen aus den unterschiedlichsten Branchen wie Medizintechnik, Energiebranche, Halbleitersektor und Automobilindustrie, wobei aktuell die Luftfahrtindustrie einen erhöhten Bedarf an additiv gefertigten Komponenten für die Zukunft sieht. Um sie zu beliefern, besitzt Toolcraft für seine AM-Technik eine der für diese Technologie noch seltenen Zertifizierungen nach Nadcap (National Aerospace and Defense Contractors Accreditation Program), dem strengen Akkreditierungs-Regelwerk der führenden Zulieferer der Luft- und Raumfahrtbranche. Dank der entsprechenden Audits und langjähriger Expertise zählen die Franken zu den Lieferanten von Serienteilen – zum Beispiel für das neue Leitschaufel-Cluster von MAN.

Mit neuem Laserkopf die Produktivität um Faktor 10 erhöht
Nach den positiven Erfahrungen mit dem pulverbasierten Laserschmelzen (Laser Metal Fusion) investiert Toolcraft auch in ein patentiertes und mehrmals ausgezeichnetes 3D-Verfahren des Fraunhofer ILT: Es handelt sich um das extreme Hochgeschwindigkeits-Laserauftragschweissen EHLA, das sich bereits mehrfach als umweltfreundliche und schnelle Alternative zum Chrom(VI)-Hartbeschichten beim Offshore-Einsatz (Korrosions-Schutz für Hydraulikzylinder) in den Niederlanden und China bewährt hat.
Der Toolcraft-Geschäftsführer hofft auf den weiteren Aufstieg des metallischen 3D-Druck, etwa durch höhere Produktivität und Automatisierung. «Auf jeden Fall muss der Bauraum noch grösser ausfallen, hier wäre ein Durchmesser von 500 mm schön», ergänzt Hauck. «Ausserdem wünsche ich mir die Möglichkeit zur Beheizung der Bauteile, um die Werkstoffvielfalt zu erhöhen.»
Antworten auf diese Wünsche bot ihm und den anderen 200 Teilnehmern der Rundgang durch das Fraunhofer ILT: Dort wurde eine skalierbare LPBF-System für XXL-Teile (1‘000 mm x 800 mm x 500 mm) vorgeführt, das dank eines neuen Laserkopfs die Produktivität im Vergleich zu üblichen LPBF-Anlagen um den Faktor 10 steigert – ein weiterer additiver Innovationssprung aus Aachen.
Kurz und knapp: ICTM
Das ICTM International Center for Turbomachinery Manufacturing in Aachen ist eine gemeinsame Initiative der Fraunhofer-Institute für Produktionstechnologie IPT und Lasertechnik ILT, des Labors für Werkzeugmaschinen und Fertigungstechnik WZL der RWTH Aachen sowie des Lehrstuhls für Digital Additive Produktion DAP der RWTH Aachen.
Ziel des ICTM Aachen ist es, im Zusammenspiel von Forschung und mittlerweile 34 Industriepartnern, technologische Innovationen zu beschleunigen und in die industrielle Anwendung zu überführen.
Alle zwei Jahre laden Fraunhofer IPT und ILT seit 2011 zur ICTM Conference ein, auf der auch die Ergebnisse der gemeinsamen Forschung vorgestellt werden. Die Mitgliedsliste liest sich wie ein Who-is-who des Turbinenbaus, denn es arbeiten sehr viele namhafte Hersteller aus allen Bereichen dieser Branche mit.
Impressum
Autor: Nikolaus Fecht im Auftrag des Fraunhofer Instituts für Lasertechnik ILT
Bilder: Fraunhofer ILT
Publiziert von Technik und Wissen (eal)
Weitere Artikel
Veröffentlicht am: